Reputable Packaging Machine Repair Service for Reliable Operations
Reputable Packaging Machine Repair Service for Reliable Operations
Blog Article
Comprehending the Trick Elements and Repair Methods for Packaging Equipment Maintenance
Reliable upkeep of product packaging makers pivots on a detailed understanding of their vital elements, including the structure, drive system, and securing mechanisms. Identifying typical maintenance concerns, combined with the implementation of preventative strategies and repairing methods, can significantly boost maker reliability. The selection of repair work techniques, including the usage of OEM parts and the value of certified service technicians, plays an essential duty in reducing downtime. To absolutely understand the details of these systems and their maintenance, one need to consider the wider effects of overlooking these necessary practices.
Secret Parts of Product Packaging Machines
Packaging devices include numerous vital components that collaborate to guarantee reliable and effective packaging processes. At the core of these makers is the frame, which offers structural integrity and houses the different operating parts. The drive system, commonly a mix of electric motors and gears, helps with the movement of components, enabling precise operation throughout the product packaging cycle.
An additional crucial part is the conveyor system, which moves items with different stages of the packaging procedure. This is commonly matched by sensors and controls that keep track of the position and rate of products, making sure synchronization and reducing errors. The filling up system is crucial for accurately giving the right amount of item into plans, whether in fluid, powder, or solid kind.
Securing mechanisms, consisting of warm sealers or glue applicators, play a crucial function in securing bundles, avoiding contamination and extending life span. Furthermore, classifying systems are important for offering necessary item information, making certain conformity with regulations. Ultimately, the control panel, equipped with easy to use interfaces, permits operators to take care of device features, monitor efficiency, and make adjustments as required, ensuring ideal productivity and effectiveness in packaging operations.
Typical Maintenance Concerns
Effective procedure of product packaging devices depends greatly on regular maintenance to avoid common issues that can interrupt manufacturing. Among these problems, mechanical damage prevails, particularly in elements like motors, conveyors, and seals, which can cause unanticipated downtimes. Additionally, misalignment of parts can result in inefficient procedure, creating items to be inaccurately packaged or harmed during the process.
Another common maintenance issue involves the build-up of dust and debris, which can conflict with the equipment's sensing units and relocating components. packaging machine repair service. This not just influences efficiency yet can additionally pose safety risks. Additionally, lubrication failures can cause boosted rubbing, causing getting too hot and ultimate part failing.
Electric issues, usually originating from loosened links or worn-out wiring, can disrupt equipment features, causing considerable production hold-ups. Last but not least, software program glitches due to incorrect configurations or obsolete programs can impede the device's operation, necessitating immediate treatment. Resolving these typical upkeep problems proactively is important view it now for making certain ideal performance and durability of packaging equipment.
Preventative Maintenance Strategies
Carrying out preventative maintenance approaches is important for maintaining the effectiveness and integrity of packaging makers. These techniques incorporate a systematic strategy to maintenance, concentrating on the normal assessment and maintenance of equipment to preempt possible failures. By adhering to a set up maintenance program, drivers can identify deterioration on parts before they cause significant break downs.
Trick elements of a preventative maintenance method consist of routine assessments, part, lubrication, and cleansing replacements based on maker referrals. Utilizing checklists can improve this process, making sure that no essential tasks are neglected. Furthermore, keeping exact documents of upkeep tasks aids in tracking the device's performance gradually, assisting in educated decision-making pertaining to future maintenance needs.
Training personnel on the value of preventative upkeep improves conformity and promotes a society of positive care. Carrying out an anticipating maintenance component, utilizing information analytics and sensor innovation, can further maximize machinery efficiency by anticipating failings prior to they happen.
Fixing Techniques
When confronted with breakdowns or ineffectiveness in packaging equipments, using methodical troubleshooting techniques is crucial for recognizing and fixing issues promptly. The very first step in reliable troubleshooting is to establish a clear understanding of the machine's functional specifications and efficiency metrics. This includes reviewing the equipment's specs, as well as any type of error notifies or codes presented.
Next, drivers ought to perform a visual examination, inspecting for obvious indications of imbalance, wear, or damages. This commonly includes taking a look at gears, belts, and sensing units to pinpoint prospective reasons of malfunction. Gathering functional information, such as production rates and downtime logs, can additionally offer understandings right into repeating concerns.
Once prospective troubles are identified, utilizing a rational strategy to isolate the origin is crucial. This may need screening individual elements or systems in a controlled way. Participating in discussions with drivers that connect with the machinery consistently can yield useful responses concerning uncommon actions or patterns.
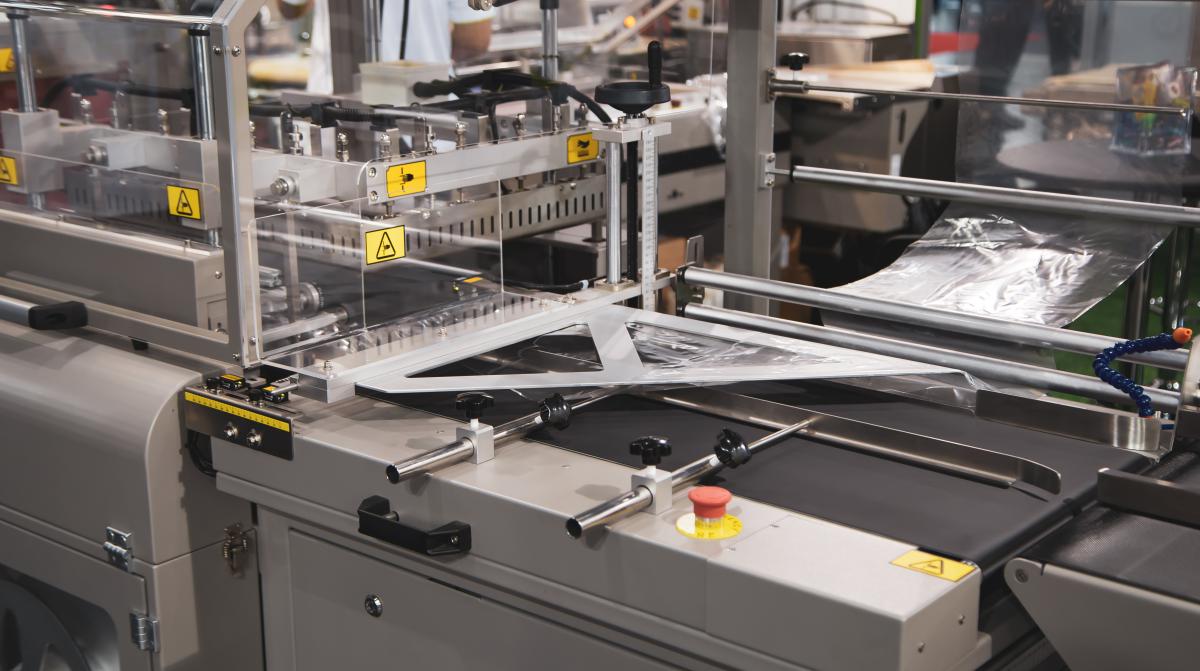
Repair and Substitute Finest Practices
A detailed understanding of repair work and replacement find more information ideal practices is essential for keeping the durability and efficiency of product packaging devices. Routinely assessing the problem of device parts enables for timely treatment, avoiding even more considerable issues that can cause expensive downtimes.
When repairs are essential, it is vital to use OEM (Original Equipment Supplier) parts to guarantee compatibility and performance. This not only preserves the stability of the machine however also maintains warranty contracts. In addition, it is recommended to keep an inventory of essential spare components to facilitate quick substitutes and minimize functional disruptions.
For intricate repair services, engaging certified specialists with specialized training in packaging machinery is advised. They have the expertise to detect problems precisely and perform fixings efficiently. Recording all repair service activities and parts replacements is essential for preserving a thorough maintenance history, which can assist in future troubleshooting.
Lastly, executing a positive strategy, consisting of regular evaluations and predictive maintenance techniques, boosts the reliability of packaging makers. By adhering to these finest practices, businesses can make certain optimal device efficiency, minimize functional dangers, and extend equipment life expectancy.

Conclusion
In conclusion, a complete understanding of product packaging maker parts and efficient maintenance techniques is essential for ideal efficiency. By implementing these methods, companies can guarantee the longevity and effectiveness of product packaging makers, ultimately contributing to improved functional performance and reduced expenses (packaging machine repair service).
Efficient upkeep of packaging machines hinges on a thorough understanding of their essential elements, including the framework, drive system, and securing devices.Reliable procedure of product packaging machines depends greatly on normal maintenance to stop usual problems that can disrupt manufacturing.Implementing preventative upkeep approaches is important for sustaining the performance and dependability of product packaging devices. Additionally, preserving accurate records click over here now of maintenance activities help in tracking the machine's efficiency over time, assisting in educated decision-making pertaining to future maintenance requirements.

Report this page